LEAN MANUFACTURING
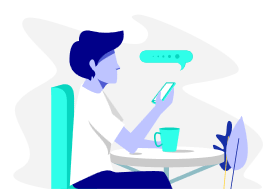
In order to make the learning effective, we have structured the program that includes the practical implementation of Learned Lean Concepts in their respective factory / work area. During our journey of Lean consulting we have developed few software that helps the factories to improve from their current state level and sustain in the improved state level. We have recommended this software in the appropriate places.
- Basic Principles of Lean manufacturing
- 5S implementation in work place. Map a process and understand its input & Output.
- Identify 7 deadly wastes& Eliminate wastes in the process. Knowledge of Kaizen.
- We recommend including MTM codes which helps to develop best methods in sewing.
- Ability to diagnose the problem present in the functional area and improve them using various lean tools and techniques such as 7 Quality control Tools, 3M, A3 thinking, JIT, Kanban, SMED, TPM, standard work, 3P, Pull system, Takt time.
- Improve company’s bottom line by leading Lean projects using Lean tools such as Value Stream Mapping, A3 plan for the organization, Kaizen events. Ability to train people in Yellow & green belts within the organization and bring Lean culture across the organization.
- Ho shin Planning, Lean Accounting