In any manufacturing industry, a good Supervisor can take a firm to incredible heights. Especially in the Garment Manufacturing Industry which is labour-intensive, the Supervisor acts as a bridge between the management and the Operators which are the pillars of the industry. Considering their critical role, the industry needs to have a technically sound Supervisor.
Committed to offering solutions for problems faced by the industry, Methods Apparel Consultancy came up with a special initiative Pro-SDP (Professional – Supervisor Development Program) thereby up-skilling the Supervisors through technology and training
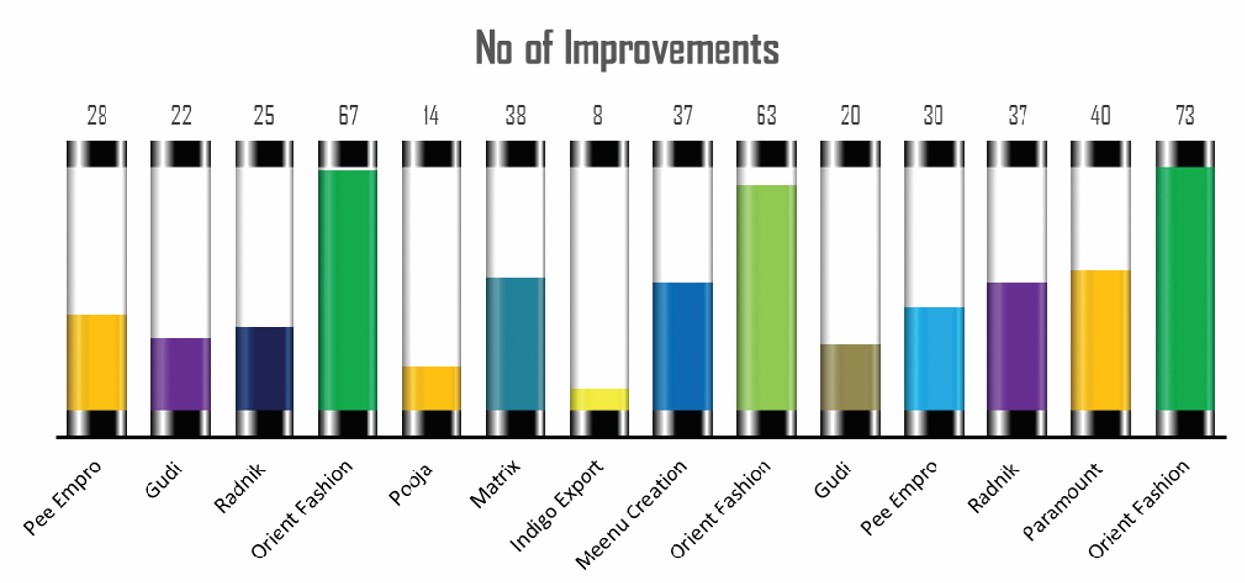
The program was successfully implemented in one of the prominent clusters in the subcontinent, the Okhla Garment and Textile Cluster (OGTC). METHODS that conducted 12 such programs and trained approx. 300 individuals that comprised 70% Supervisors,15% Sub-Supervisors, 15% Quality IE or Floor- in-charges from prominent Export Houses namely Pee Empro, Gudi Exports, Paramount Products, Meenu Creations, Orient Fashions, Matrix Clothing, Indigo Export, Radnik and Pooja International
The training spanning a 120 hour program (with 40 hours theory and 80 hours practical training for Supervisors) was focused on the overall development of Supervisors, giving them an insight into how to deal with real-time problems in a more systematic and structured manner. It is worth a mention that the industry in the past has been focusing more on either targeting the Operator or the Higher Management with little or negligible training provided to the Supervisors. METHODS, upon realizing the importance of the middle management in the Sewn Product Industry thus designed Pro-SDP, keeping in mind the needs and requirements of the Supervisor

Special Program for Assistant Supervisors.
One of the special highlight of the training module was the Assistant Supervisor Development program, with a special batch from Pee Emprowherein 25 female sewing machine operators were chosen to be promoted as Assistant Supervisor. The course was specifically customized for this group where a lot of basic knowledge was given to this group and the following topics were additionally taught that included:
- Overall flow of the orders
- How a garment factory runs
- What is an assembly line
- Functions of various departments in the garment manufacturing value chain
- PP meeting and Pilot run
- Basics of Quality and role of the Supervisor in this respect
- How to read a measurement sheet
- Understanding a Techpack
- Customer’s perspective
- Productivity and Production
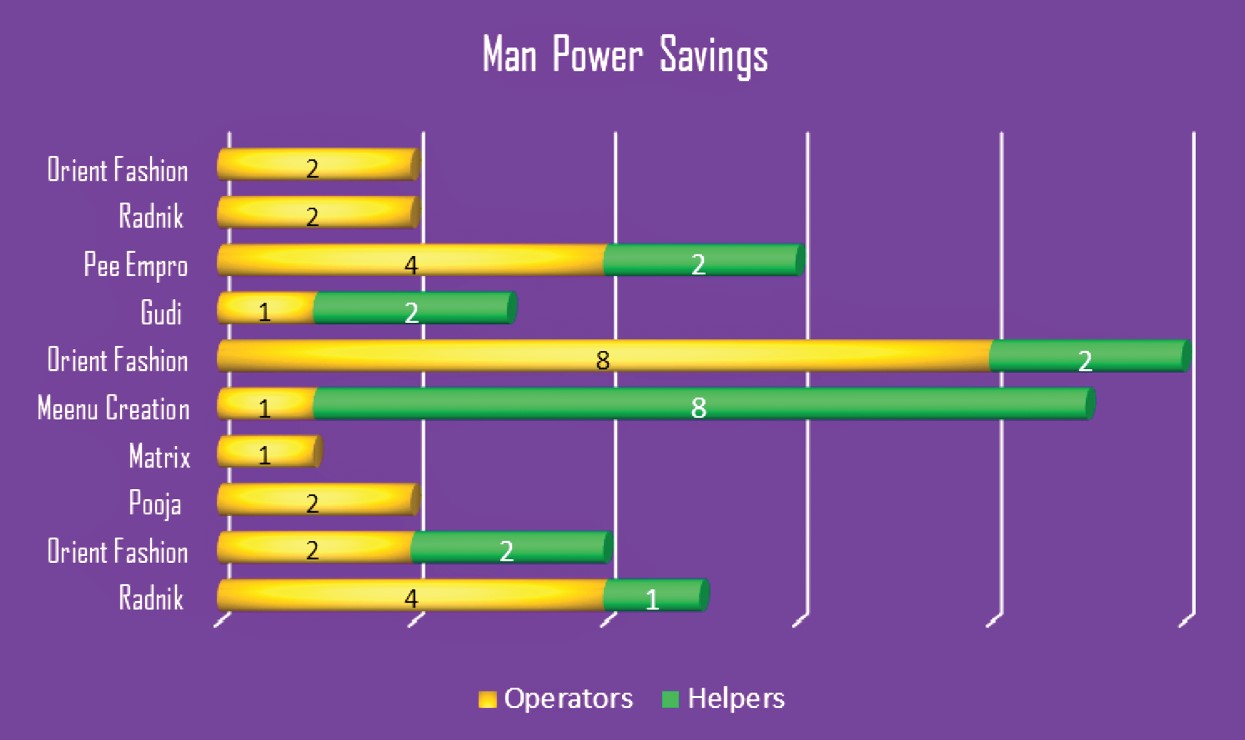
Major achievements of the Program
These were measured by implementing concepts such as PASTA, TIMWOOD, 5S, KAIZEN, JIT and JIDOKA that were learnt during the theory training and the achievements and outcome were drawn based upon data from reports and analytics on following parameters:
- Overall average improvement in efficiency
- Average improvement production
- Reduction in Manpower
- Optimising Line balancing efficiency
- Reducing overall absenteeism
- 5S implementation
- Identifying waste and eliminating waste
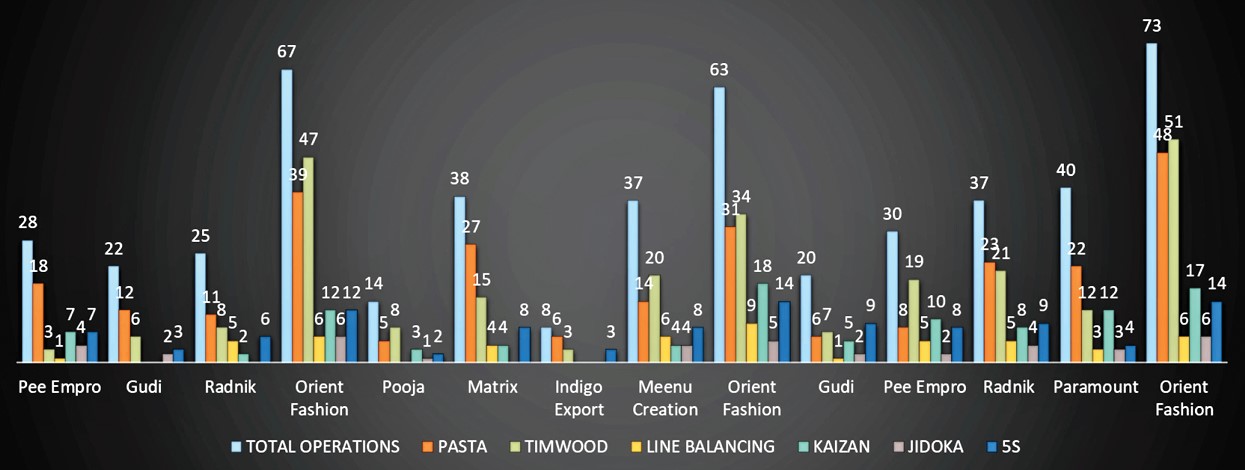
Behavioural changes
- Communication & Motivation: Improving communication to increase efficiency and motivating operators by encouraging open dialogues to foster an environment of collaborative problem-solving
- Team Work: By designing the training in a team format including practical training in specific areas of the factory, the teams strived to make improvements for their respective teams and constructively competed with each other to achieve their goals
- Preventing Absenteeism: With the Industry grappling with the absenteeism for past so many decades, the program also emphasized the need to move on from unauthorized absenteeism to authorized and informed absenteeism
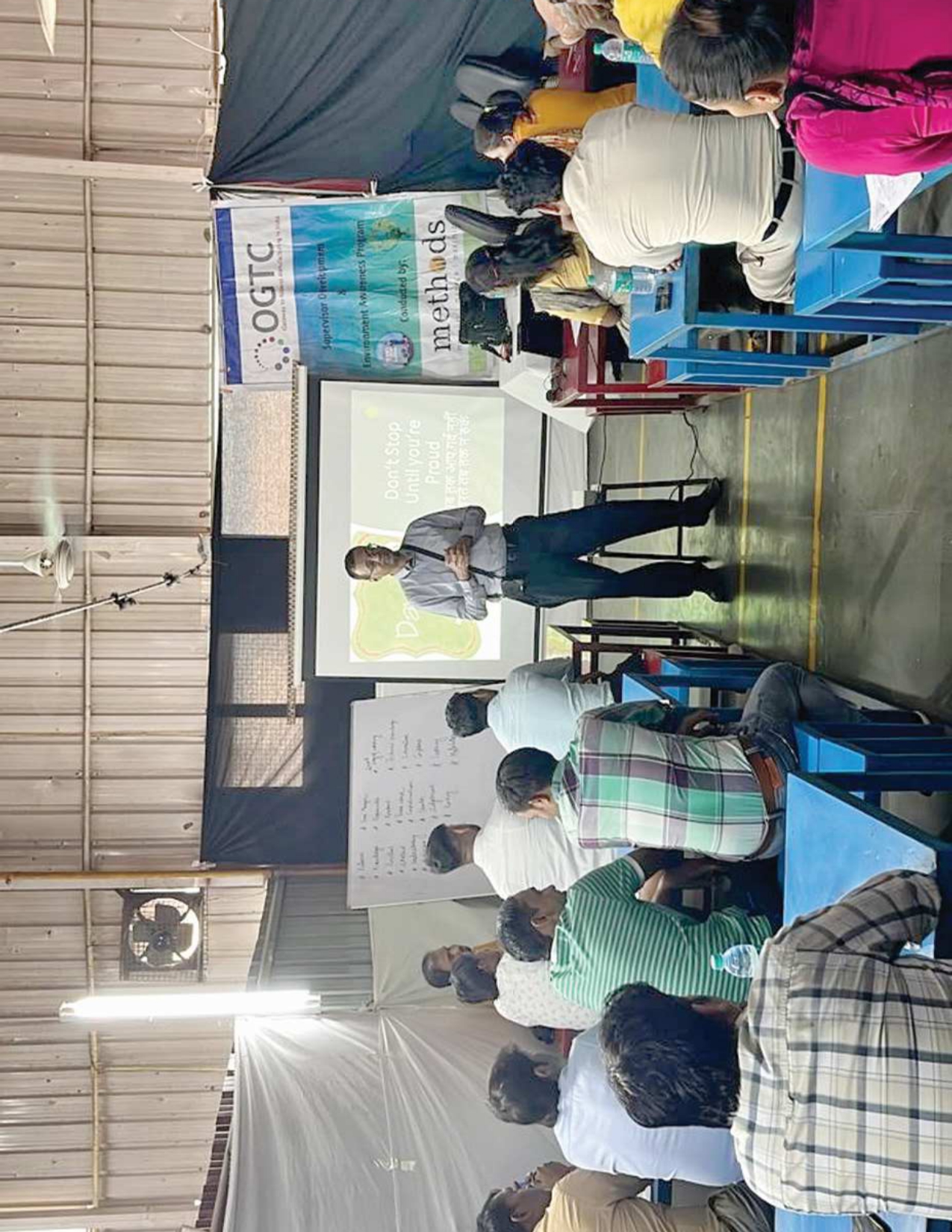
Training Methodology
- The first two weeks focused extensively on strengthening the fundamentals of the Sewn Product Industry, the program started with a general introduction and pre-assessment of candidates to know their capacities, experience and current state to establish their potential learning gaps and to gauge the level of trainees so that the learning pace and subjects can be adapted to their aptitude.
- An ice-breaking session was done to establish communication between the participants and the trainer to attain a comfort level. An overview of the complete program was given to all followed by an open session where participants listed down their learning outcome from the program. The first module was focused on opening up their minds and inspiring them to become creators rather than followers through a series of videos, activities, and storytelling and they became much more receptive to new ideas.
- With an open they were ready for learning, up-skilling, and re-skilling as the roles and responsibilities along with their positioning in the value chain were discussed in detail. They were further engaged through brainstorming sessions and activities so they can deliver the best results. Other important aspects covered in this training were Lean Manufacturing, Industrial Engineering and Line Balancing. It was mesmerizing to see them learning how to calculate operators’ capacities, check their efficiencies, and balance their lines through data-driven facts.

Final presentation by the participants
- The learning outcomes were finally presented to the management by the teams and in fact each individual came forward and shared the learning experiences as well as showcased their improvements in a Before and After video. This was a really interactive program which honed their communication skills and it was pleasantly surprising to watch them speak confidently. Their leadership skills were also developed as each team also chose a leader among themselves. Finally, all participants were awarded certificates for successful completion of training.
- All in all, the ethos on which this program runs is; There is no best way, there is always a better way or as they say in Hindi; Sarvottam mein bhi Sudhar Sambhav Hai. This is the philosophy of the program where each person is prepared to make changes and do continuous improvements in whatever task they perform.
- With an open they were ready for learning, up-skilling, and re-skilling as the roles and responsibilities along with their positioning in the value chain were discussed in detail. They were further engaged through brainstorming sessions and activities so they can deliver the best results. Other important aspects covered in this training were Lean Manufacturing, Industrial Engineering and Line Balancing. It was mesmerizing to see them learning how to calculate operators’ capacities, check their efficiencies, and balance their lines through data-driven facts.
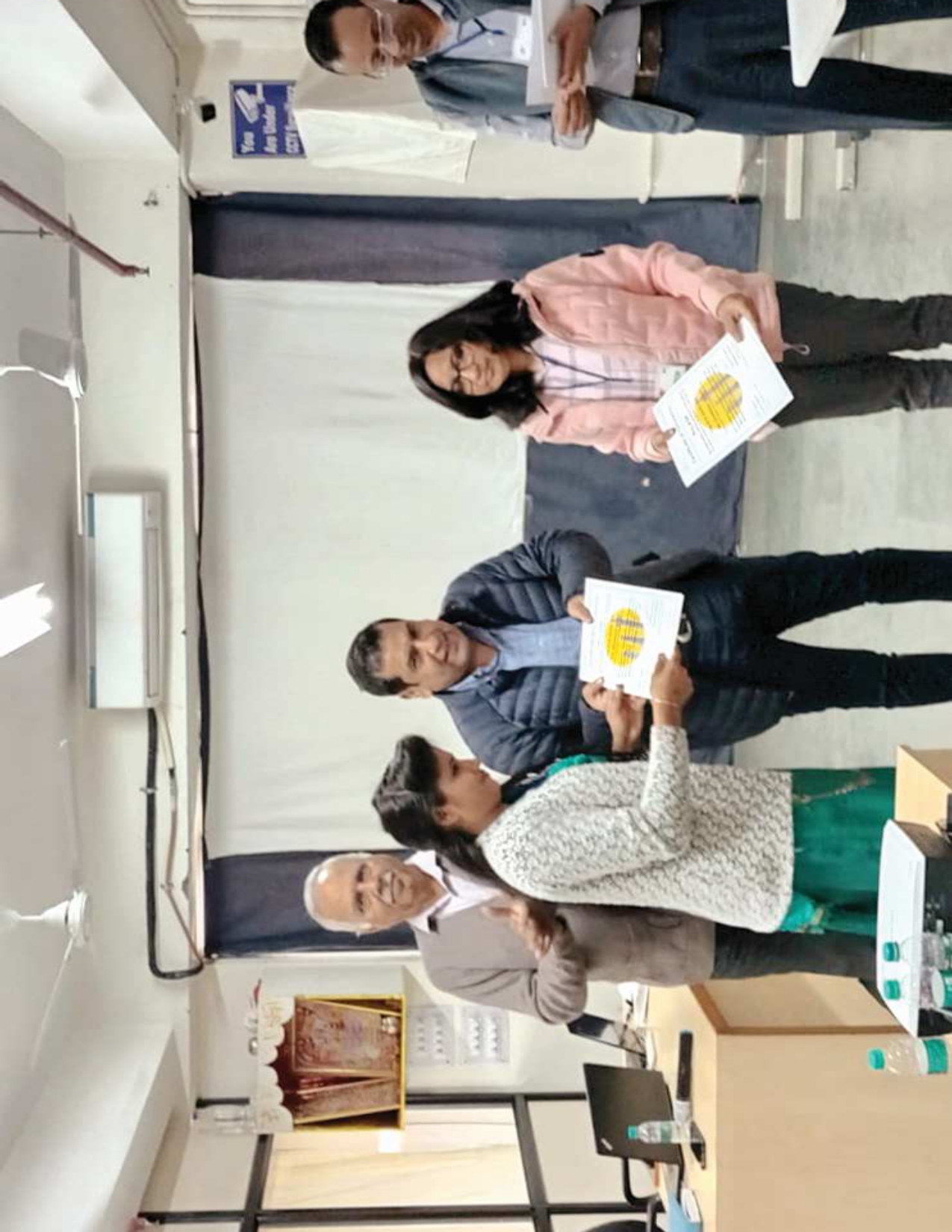