The global apparel industry is a behemoth, with countries like China, Bangladesh, Vietnam, Germany and India at its forefront. These nations have long been the epicenter of garment production, driving economic growth and providing livelihoods to millions.
When we scrutinize the production efficiency of the Apparel Industry in India, it becomes evident that the industry as a whole has fallen short of achieving optimal production goals. This inefficiency trickles down through various stages of production, from cutting to final stitching. In this blog, we will delve into the underlying issues plaguing the Apparel Industry in India, shedding light on the critical need for a transformative approach.
The Manufacturing Conundrum
Despite the industry's prominence, it faces a glaring issue: inefficiency in the apparel manufacturing value chain system. From fabric to packaging of the final product, there are numerous challenges in the value chain of the Indian apparel manufacturing industry, including smaller run sizes, a shallow or long learning curve, high absenteeism, fabric defects including bowing, shrinkages etc, lack of scientific approach in the cutting room, lack of real-time efficiency data, and untrained or incompetent middle management, among others.
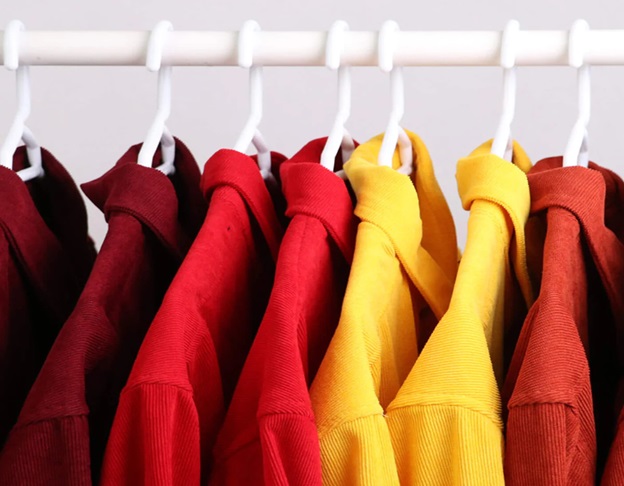
This results in inefficiency & low productivity, further leading to longer lead times and increased manufacturing costs, that hinder the growth of the workforce, company, and the industry as a whole.
Fabric Delivery & Quality: A Concern
Fabric is a key component of a garment, the quality of which affects garment production directly. Fabric quality has a lot of concerns, including bowing, shrinkage issues, lot variations, uneven width, inconsistent printing, along with regular fabric defects, especially when it comes to fabric produced in India by the powerloom sector.
On-time fabric delivery is another issue that is prevalent in the industry, mainly due to the lack of a reliable fabric supply chain. The fabric in a lot of cases arrive post the scheduled arrival date, leaving minor to no room for a proper quality check, thus affecting the quality of the end product and the organisation negatively.
Due to the huge investment that goes into fabric production, there are limited suppliers that the sewn product industry has to rely upon. It has further been witnessed that this one-sided dependency has in some cases led to a lack of accountability on the supplier's end, which hurts the sewn product industry directly. It is the need of the hour to spend on the R&D aspects of fabric and further sort the issues about the quality of the fabric.
Optimisation Of The Cutting Room: Deprioritised
Cutting is a crucial process in apparel production and accounts for 60% to 70% of the total cost of basic-styled garments. It sets the foundation for the entire garment, determining its fit, quality, and overall appeal.
If there is one department in the sewn product industry that lacks a scientific measure of its processes today, it is cutting. The factories often ignore the efficiency of the processes involved in cutting, as the production floor drives the cutting room, thus deprioritizing its efficiency.
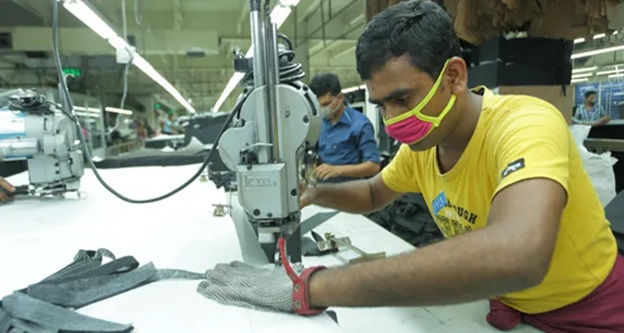
However, there is a lot of potential when it comes to increasing the efficiency and productivity of the cutting room. Proper cut order planning, accountability of every single centimeter of fabric, monitoring fabric wastages, end bits and end losses, curbing roll variances and instilling stronger fabric disciplines can lead to fabric savings.
Reducing fabric wastages not only benefit the factory financially but also enriches the company's commitment to sustainability, thus ranking them higher on the Environmental, Social, and Governance (ESG) index.
Production Floor: Far From Being Efficient
In addition to cutting, the stitching phase of production is equally important. This stage of apparel production gets the maximum attention but the majority of inefficiencies belong to the stitching process. This is the leading process in garment manufacturing, employing the maximum number of resources. Inadequate training of sewing machine operators, a lack of standardised processes and data availability, inefficient QC mechanisms, lack of QCO practices, long learning curve, mindset of the management, and high attrition & absenteeism contribute to lower productivity & higher DHU.
Streamlining the stitching process through the adoption of data-driven technology and comprehensive training programmes and process re-engineering through Lean Manufacturing can greatly enhance production efficiency.
The Way Forward: A Paradigm Shift
To address these inefficiencies, a paradigm shift is imperative and the mindset of the management is of utmost importance in driving the shift. For instance, when it comes to the learning curve, on one hand we have witnessed factories achieving 2nd day peak and on the other side factories are planning a 15 day learning curve to reach up to 75%. Thus concluding that the mindset and expectations of the management play a very critical role in deciding the learning curve and further influence the overall efficiency. Not to forget that trained middle management, production planning, strong discipline, lean concepts along with well developed SOPs are required to achieve better results.
In addition to effective management, the apparel industry must embrace real time data capturing, training, and innovation across all stages of production. This includes investing in data-driven solutions (including personalised data tracking), strengthening HR practices to curb absenteeism and further establish a steep learning curve, enabling a standard QMS, and implementing robust training programmes to upskill the workforce.
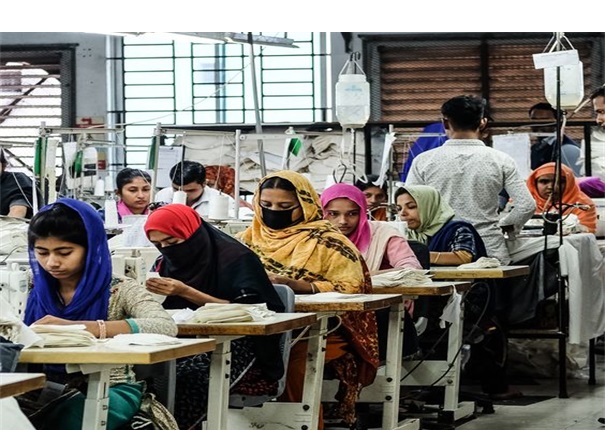
Conclusion
The apparel industry stands at a pivotal juncture, where addressing inefficiencies is paramount for its sustained growth and competitiveness. By recognising the critical areas of improvement in its production processes, cutting and stitching, and implementing transformative measures, the industry can unlock new levels of efficiency and profitability. Through collective efforts and a commitment to training, data, and continuous improvement, the apparel industry can not only meet but surpass its production goals, ensuring a brighter and more sustainable future for all stakeholders involved.